- Moderator
- #1
Disclaimer: This is my first attempt at reshafting irons... The intention here is to just share my experiences, not as a perfect guide to the reshafting process. There are plenty of incredible videos out there done by PGA Professionals who have been reshafting for years.
The Goal
So I've been talking around the forum about re-shafting my j33's (currently with the Dynamic Gold SL s300 shafts) with a set of KBS Tour Black Nickel X flex shafts. The end goal will be 3/4" longer than standard which is set on Bridgestone's site for J33's
Specifications
To my understanding, adding a 1/2" inch to a club will mean they will sit about 1* flat at address, which I'm good with. I may consider having them bent 1* strong eventually, but that won't be a part of this.. I just wanted to document the process for anyone considering doing some reshafting at home.
The Goods
In order to get this done, I had to pick up the following pieces of equipment -- I'm basically going from scratch on a lot:
- Four shaft extensions - both sides can be used, so four extensions = 8 shafts (Golf Galaxy, GolfSmith, etc)
- hacksaw to cut extensions (home depot, Lowes)
- Mitre board in order to cut the shafts dead straight (Home Depot, Lowes)
- Sand paper + screwdriver (I'd prefer a wire brush but couldn't find one locally)
- heat gun (or torch, that's optional)
- epoxy (I'd avoid the quick set personally)
- ferrules (cell-parts is an awesome option)
- work gloves
Removing the Old Shafts
Steel shafts are quite a bit easier than graphite and you can spin them as the epoxy bond weakens. I would encourage spinning after a decent amount of heat as it takes quite a bit less time, especially with the convenience of the grip on there. Make sure to use a work glove or heat protected glove on the hand holding the clubhead because it definitely heats up!!!!
This process is really quite simple. My Wagner heat gun has two temps (750* and 1000*) and I ran it at 1000* with no issues.. Some folks like to use a torch for this process but I also play hockey so I opted to buy the heat gun because it works well on replacing blades on hockey sticks.
Some shafts have small weights on the ends of them (visible in the photo below), and they can get left behind after the original pull. Rather than drilling them out like some videos suggest, add a bit of heat higher up on the hosel, and slowly start to knock away the extra epoxy around it in the hosel. Then use something 'like' a drill bit to get inside the weight and start twirling it. That should eventually make it loose enough to be tugged out.
The next step is to clean out the hosel of any remaining epoxy. I'm going to keep uploading as I continue the process and I'll edit everything into this post. I hope anyone considering club building finds this beneficial and those who are pros can chime in with better practices.. Right now it's a mix and match of the most effective ways I've read about.
The Goal
So I've been talking around the forum about re-shafting my j33's (currently with the Dynamic Gold SL s300 shafts) with a set of KBS Tour Black Nickel X flex shafts. The end goal will be 3/4" longer than standard which is set on Bridgestone's site for J33's
Specifications
|
To my understanding, adding a 1/2" inch to a club will mean they will sit about 1* flat at address, which I'm good with. I may consider having them bent 1* strong eventually, but that won't be a part of this.. I just wanted to document the process for anyone considering doing some reshafting at home.
The Goods
In order to get this done, I had to pick up the following pieces of equipment -- I'm basically going from scratch on a lot:
- Four shaft extensions - both sides can be used, so four extensions = 8 shafts (Golf Galaxy, GolfSmith, etc)
- hacksaw to cut extensions (home depot, Lowes)
- Mitre board in order to cut the shafts dead straight (Home Depot, Lowes)
- Sand paper + screwdriver (I'd prefer a wire brush but couldn't find one locally)
- heat gun (or torch, that's optional)
- epoxy (I'd avoid the quick set personally)
- ferrules (cell-parts is an awesome option)
- work gloves
Removing the Old Shafts
Steel shafts are quite a bit easier than graphite and you can spin them as the epoxy bond weakens. I would encourage spinning after a decent amount of heat as it takes quite a bit less time, especially with the convenience of the grip on there. Make sure to use a work glove or heat protected glove on the hand holding the clubhead because it definitely heats up!!!!
This process is really quite simple. My Wagner heat gun has two temps (750* and 1000*) and I ran it at 1000* with no issues.. Some folks like to use a torch for this process but I also play hockey so I opted to buy the heat gun because it works well on replacing blades on hockey sticks.
Some shafts have small weights on the ends of them (visible in the photo below), and they can get left behind after the original pull. Rather than drilling them out like some videos suggest, add a bit of heat higher up on the hosel, and slowly start to knock away the extra epoxy around it in the hosel. Then use something 'like' a drill bit to get inside the weight and start twirling it. That should eventually make it loose enough to be tugged out.
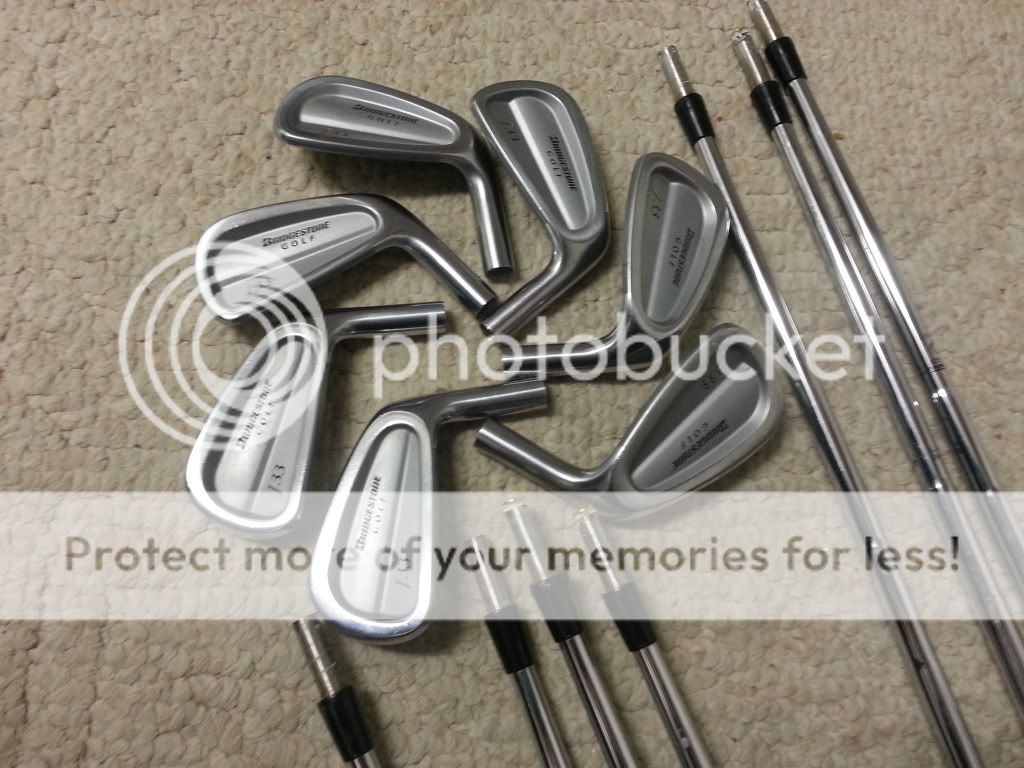
The next step is to clean out the hosel of any remaining epoxy. I'm going to keep uploading as I continue the process and I'll edit everything into this post. I hope anyone considering club building finds this beneficial and those who are pros can chime in with better practices.. Right now it's a mix and match of the most effective ways I've read about.
Last edited: